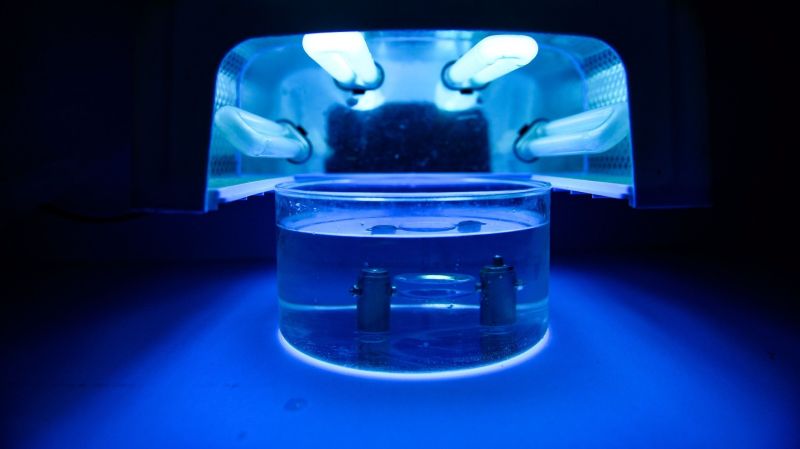
Traditional lensmaking is a grind — literally. One starts with a piece of glass, rubs it against an abrasive surface to wear away the excess bits, and eventually gets it to just the right shape and size for the job. Whether done by machine or by hand, it’s a time-consuming process, and it sure seems like there’s got to be a better way.
Thanks to [Moran Bercovici] at Technion: Israel Institute of Technology, there is. He leads a team that uses fluids to create complex optics quickly and cheaply, and the process looks remarkably simple. It’s something akin to the injection-molded lenses that are common in mass-produced optical equipment, but with a twist — there’s no mold per se. Instead, a UV-curable resin is injected into a 3D printed constraining ring that’s sitting inside a tank of fluid. The resin takes a shape determined by the geometry of the constraining ring and gravitational forces, hydrostatic forces, and surface tension forces acting on the resin. Once the resin archives the right shape, a blast of UV light cures it. Presto, instant lenses!
The interface between the resin and the restraining fluid makes for incredibly smooth lenses; they quote surface roughness in the range of one nanometer. The use of the fluid bed to constrain the lens also means that this method can be scaled up to lenses 200-mm in diameter or more. The paper is not entirely clear on what fluids are being used, but when we pinged our friend [Zachary Tong] about this, he said he’s heard that the resin is an optical-grade UV adhesive, while the restraining fluid is a mix of glycerol and water.
We’re keen to see [Zach] give this a try — after all, he did something similar lately, albeit on a much smaller scale.
Molding Complex Optics in a Completely Fluid System
Source: Manila Flash Report
0 Comments